Clay Resist Printing
- Rheanna Gilbert
- Dec 19, 2020
- 3 min read
First semester is drawing to a close and it’s hard to believe that I am now halfway through my capstone! I’m so proud of how far I’ve come, even though anxiety about the big deadline is beginning to set in. There is still lots of time before April though, and I’m excited to dive into wooden block making come January.
In my print sampling frenzy over the last few weeks, the technique I have most connected with (and got great results with) is clay resist printing with indigo dyeing. Honestly, this is unsurprising since I have expressed my love for indigo in the past and it hasn’t faded one bit. This post is all about the process of clay resist printing from mixing the paste, to the end result of a beautiful blue and white eye pillow.
The process begins with a relatively simple mixture of water, gum arabic, magnesium sulphate (epsom salts), bentonite clay, and kaolin clay. I love the simplicity of this recipe, with all of the ingredients being common in either food or beauty products.
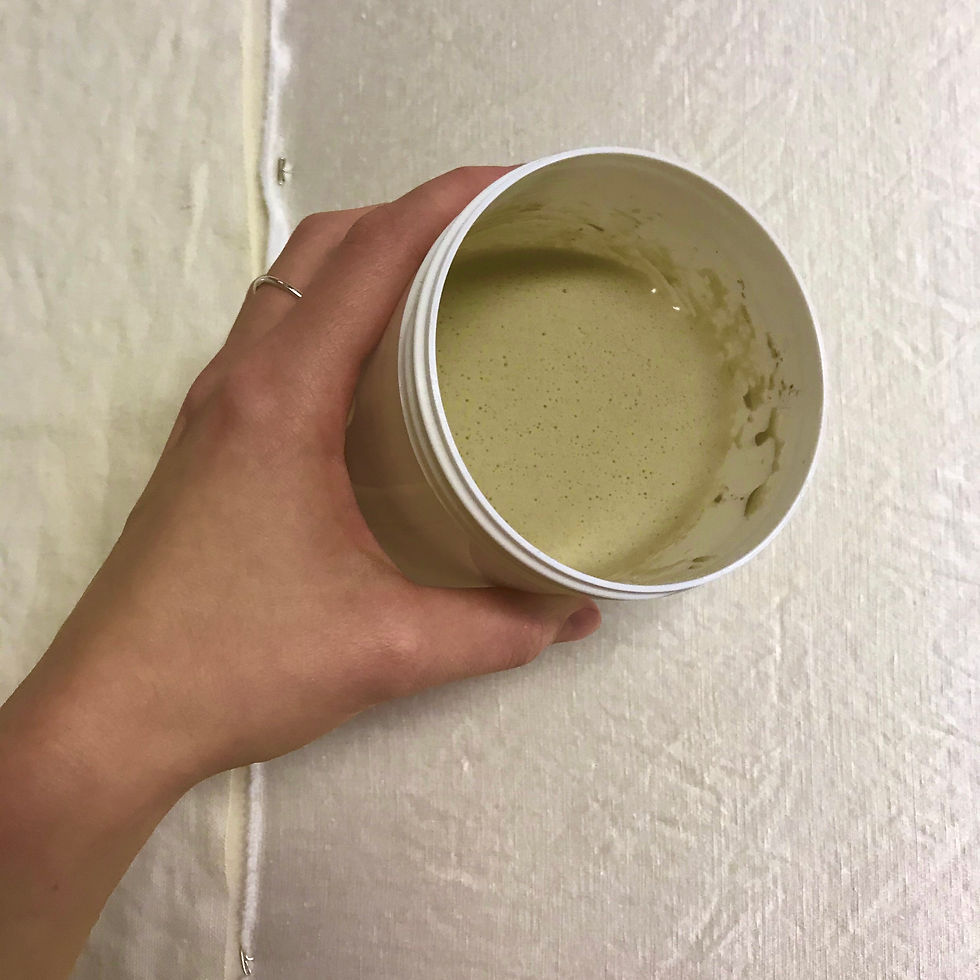
Fig. 1 Prepared clay resist paste
Next comes the printing! Initially I was dabbing the paste onto the block with a small makeup sponge, but later discovered the much more effective method of soaking a small piece of upholstery foam (or a kitchen sponge) with the paste and stamping the blocks onto it like an ink pad. After inking, I stamp the block onto the fabric and give it a couple swift whacks with the side of my hand (yes, it is sore). I try to employ printing techniques that I was shown in India as much as I can. I figure after hundreds of years of block printing, they probably know best.
Pictured below (centre) is a technical sample, demonstrating the results of layering a print multiple times to achieve a better resist. It also compares the lino block print to a wooden block print (along the right edge of fabric), and the results when additional clay is added (top half). The left photo showcases the common occurrence of puckering fabric as the resist dries, particularly when larger areas are printed.

Fig. 2 Left to right: printing block of an indigo branch, printed sample, a dried printed sample
On to my favourite stage… the indigo dip! After waking up my vat with a gentle heating, generous stir, then a rest, I place the cloth into the vat. With this process, the fabric cannot be wetted out before dyeing because the resist dissolves very easily in water. The alkalinity of the indigo vat allows the paste to remain intact until the fabric is ready to be washed.
Fig. 3 Rheanna stirring the indigo vat to “wake it up”

Fig. 4 Indigo dipped sample oxidizing
The clays can clog plumbing so it is best to rinse the paste off in a bucket and bring it outside where the soil can enjoy it. If it were summer, I think it would be lovely to dye outside and just hose off the fabric, but alas, that will have to wait until spring. As you can see, once the resist is washed away, the fabric boasts a beautiful blue and white pattern! I’m in love with the results.

Fig. 5 Washed and dried technical sample
After extensive sampling, I conducted this process on a piece of hemp/silk fabric and sewed it into an eye pillow.
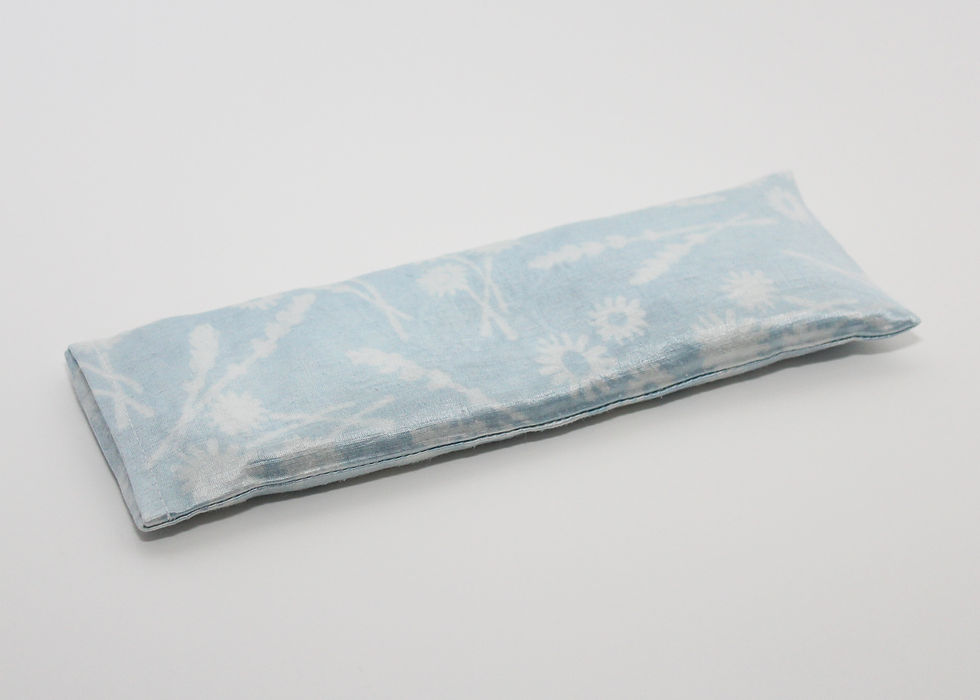
Fig. 6 Clay resist printed and indigo dyed eye pillow with flaxseed fill
It’s so exciting to see an example of what one of my capstone pieces may look like! The pattern needs some more refinement and the final pieces will likely be at least two colours, but I think this is a beautiful object and I’m looking forward to what comes next. Talk to you in the new year!
Fig. 1 Gilbert, Rheanna. “Prepared clay resist paste” 2020, Photograph.
Fig. 2 Gilbert, Rheanna. “Left to right: printing block of an indigo branch, printed sample, a dried printed sample” 2020, Photograph.
Fig. 3 Gilbert, Rheanna. “Rheanna stirring the indigo vat to ‘wake it up’” 2020, Video.
Fig. 4 Gilbert, Rheanna. “Indigo dipped sample oxidizing” 2020, Photograph.
Fig. 5 Gilbert, Rheanna. “Washed and dried technical sample” 2020, Photograph.
Fig. 6 Gilbert, Rheanna. “Clay resist printed and indigo dyed eye pillow with flaxseed fill” 2020, Photograph.
Comments