Adventures With Printing Blocks
- Rheanna Gilbert
- Dec 4, 2020
- 4 min read
The imagery involved in my capstone project is obviously integral, but the means of creating that imagery are equally important to me. I have written in previous posts about my explorations in natural dyes and my intentions behind using them, but I’ve yet to delve into my second image-making tool: printing blocks.
What better place to begin than the start of my block printing journey? In my first year at Sheridan, I carved a block from “softoleum”, which is essentially soft, easily carve-able linoleum, which I will refer to as simply linoleum in this post. I really enjoyed the technique, the process, and the results, but I didn’t fall madly in love with it… yet.

Fig. 1 First block print made in early 2018 that I’m still proud of today.
In February of 2020 (right before the pandemic really hit hard), I was lucky enough to embark on a life changing trip to Rajasthan, India, through Sheridan. For centuries, India has been recognized for their incredible block printed fabric and expertise with natural dyes. Although chemical dyes and synthetic pigments have overthrown natural dyes in most (but not all) print studios, block printing has remained central to textile craft in India. The hand-printed cloth is remarkably beautiful and holds so much character and history. Everyone loves the fabric, but what about the blocks? They’re works of art in and of themselves! Some are worked in brass, but most are hand-carved in teak wood by skilled artisans. Seeing the entire process from creating to printing with the blocks, in settings where the ancient history of this technique is palpable, really sparked my love for block printing.

Fig. 2 (left) Block carver in India
Fig. 3 (right) Me, block printing in India under the guidance of a professional block printer
Freshly inspired by my travels, I was determined to get printing, but COVID-19 had other plans. When the remainder of last semester moved online, I made the best of it by “carving” my designs into styrofoam plates and printing them with acrylic paint. Considering the circumstances, I think they turned out pretty well! Thankfully, I wasn’t dissuaded by this little hiccup, but fell even deeper in love with blocks thanks to their accessibility and flexibility.

Fig. 4 My second endeavour in block printing, using materials from the home due to the first pandemic lockdown
At last, I got my hands on a nice big piece of linoleum for my capstone project and have been carving many single-motif blocks to use in my technique sampling. In the next few days, I will finally begin to use these beauties to print clay resist paste for indigo-dyeing, print mordants, and finally print dye paste. These experiments will eventually lead me to a collection of surface designs, which I will put into repeat and carve into large wooden blocks. As much as I love the ease of linoleum blocks, they lack a certain charm. To my eye, the prints lack the character that wooden blocks give and they lose some of block printing’s rich history.
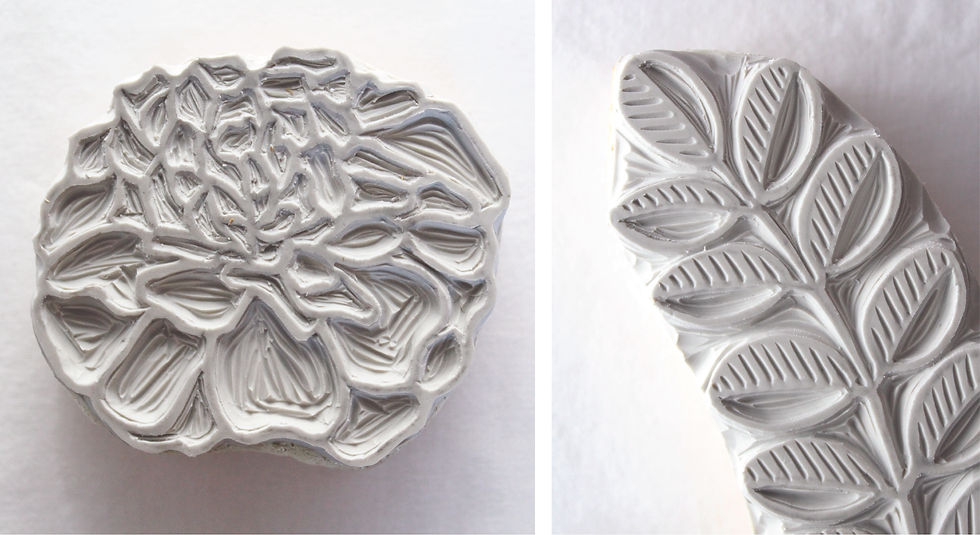
Fig. 5 Linoleum blocks of a marigold and indigo sprig, carved for my capstone project

Fig. 6 (left) Linoleum blocks carved for my capstone project
Fig. 7 (right) Test print of linoleum blocks on paper
Initially, I was hoping to have the wooden blocks carved in India, but given the state of the world this year, it doesn’t seem feasible at this time, so I decided to carve them myself. Speaking with the head of Sheridan’s furniture department, Peter Fleming, was incredibly helpful for figuring out the technicalities involved in carving wooden blocks. Although I was super resistant to the idea of using the CNC router machine (I felt that it didn’t fit with my work’s emphasis on history and hand-craft), Peter convinced me that letting the machine tackle some of the work wouldn’t degrade the integrity of my concept. It also makes more sense logistically for my time-frame and experience level. So, my current plan of action for the printing blocks is to create my repeat designs, create a digital file that the machine can read, let the machine cut out the basic shapes, and go in with small chisels and gouges to refine the block by hand. I think this is a nice compromise to achieve the history and character I am looking for in my work, while allowing modern technology to lighten my workload.

Fig. 8 Example of a CNC router cutting details into a block of wood
Although the final blocks feel like a long way away, I thought it was pertinent to address this important element of my project before my natural dye sampling takes centre stage. To me, the blocks are an intrinsic part of the finished work and I plan to display them alongside my textile goods like the piece of fine craft that they are.
Fig. 1 Gilbert, Rheanna. “Block printed tote bag” 2019. Photograph.
Fig. 2 Singh, Stephanie Angela. “Block carver in India” 2020. Photograph.
Fig. 3 Singh, Stephanie Angela. “Rheanna block printing in India” 2020. Photograph.
Fig. 4 Gilbert, Rheanna. “Styrofoam printing blocks and printed fabric” 2020. Photograph.
Fig. 5 Gilbert, Rheanna. “Linoleum marigold and indigo outline printing block” 2020. Photograph.
Fig. 6 Gilbert, Rheanna. “Linoleum printing blocks” 2020. Photograph.
Fig. 7 Gilbert, Rheanna. “Test print of linoleum blocks” 2020. Photograph.
Fig. 8 Prajapati, Vinay. “CNC Cutting: What You Need to Know About the Service.” Techprevue, 15 Feb 2020, www.techprevue.com/cnc-cutting/.
Special thanks to Peter Fleming for his insights and advisement.
Comments